Ion Sources
Linear Modular End-Hall Ion Sources
Home» Ion Sources » Gridless End-Hall Ion Sources » Linear Modular End-Hall Ion Sources
The EHL200-X and EHL400-X modular linear ion beam source is designed for applications utilizing moving flat substrates like for glass, web or foil coatings.
The eH Linear ion source is a new, innovative and successful approach to meet the requirements for a linear ion beam application. The linear modular ion sources use the eH200 and eH400end-Hall sources as the building block. A low cost linear-arrayed ion source can be constructed to accommodate a variety of substrate widths. The array configuration can permit linear ion source lengths up to approximately 1 meter. The flexibility to space the modules in the proper location is significantly beneficial towards achieving the optimal ion current doses, uniformity and process rates. Since the modules are operated in parallel, this technology simplifies the gas, power and electron distribution. Because the eH Linear product uses standard end-Hall modules, the technology minimizes equipment requirements, resulting in a cost effective, high current, low energy ion beam source available for web coating, in-line deposition, and cylindrical rotary sputtering systems.
Applications
- Ion Beam Assisted Deposition (IBAD)
- In-Situ Substrate Precleaning
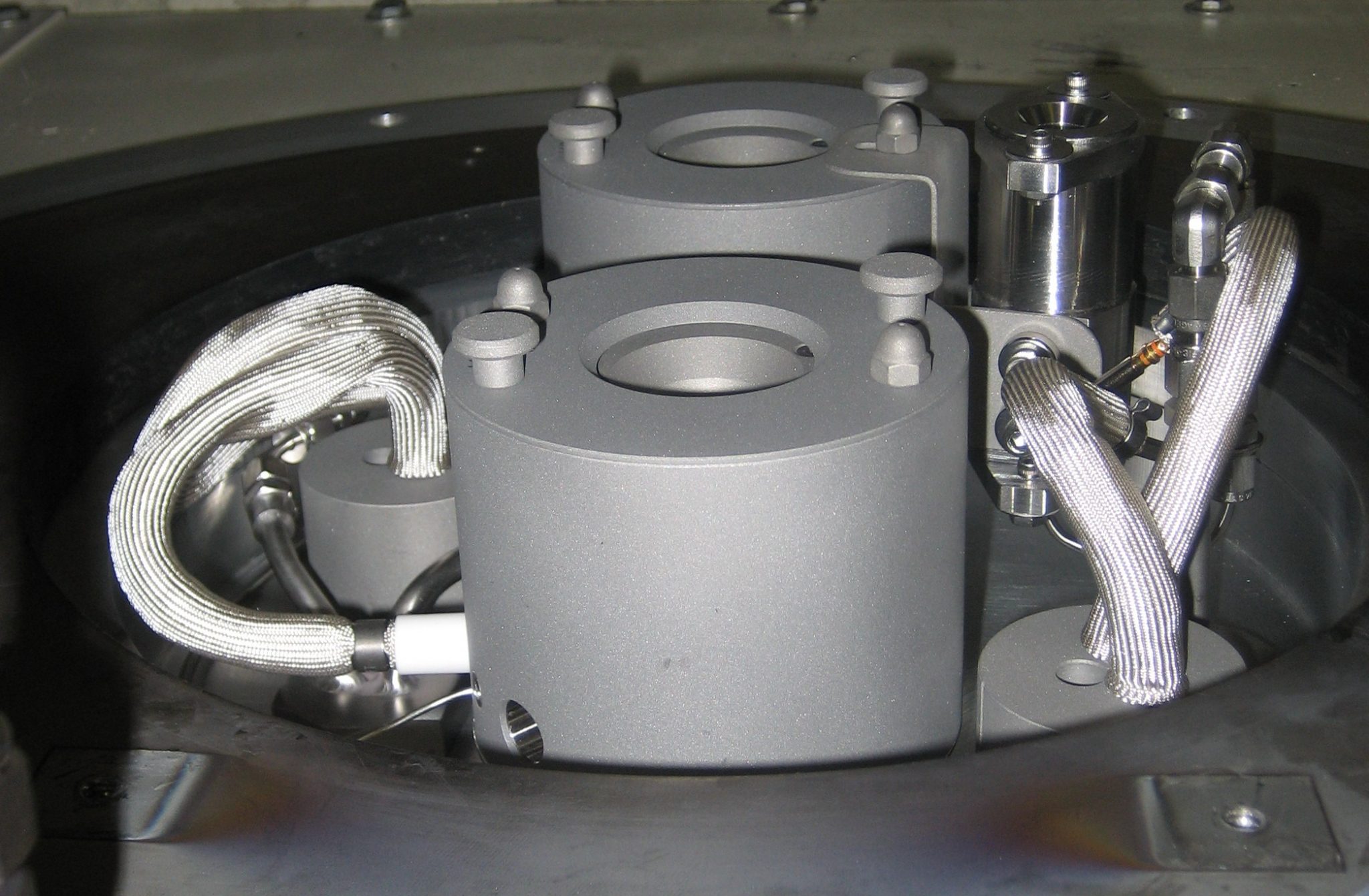

Conventional linear ion beam source
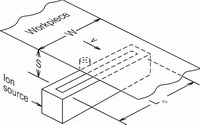
A single linear ion beam source is used to process the substrate area.
- High gas consumption
- Inflexible arrangement
- Thermal expansion issues
- Limited operating range
Modular linear ion beam source
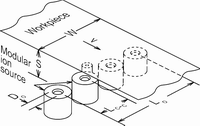
Cylindrical ion beam sources are lined up to an array
- High beam current
- Flexible module arrangment
- Large operating range
- Fully neutralized ion beam
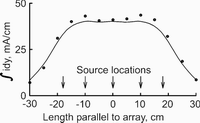
The EHL200-X modular linear source array enables for uniformities of +/- 5% over more than 80% of the source length at 30cm source-to-substrate distance.
Available models
- eHL400-2, eHL200-2
- eHL400-3, eHL200-3
- eHL400-4, eHL200-4
- eHL400-5, eHL200-5
- eHL400-X, eHL200-X
eHL200-5 | eHL200-10 | |
---|---|---|
Systemaufbau | 5 eH200 gitterlose Ionenquellen mit einer Hohlkathode | 10 eH200 gitterlose Ionenquellen mit einer Hohlkathode |
Anodenstrom | 0 - 10 A | 0 - 20 A |
Strahlstrom | 0 - 2300 mA | 0 - 4600 mA |
Anodenspannung | 60 - 225 V max | 60 - 225 V max |
Mittl. Strahlenergie | 35 - 160 eV | 35 - 160 eV |
Gasfluss | 5 - 100 sccm | 5 - 100 sccm |
Druck | 0,5 - 1x10-3 mbar | 0,5 - 1x10-3 mbar |
Länge | 360 mm | 860 mm |
Höhe | 60 mm | 60 mm |
Homogenität | +/- 5% über 30 cm bei 30 cm Abstand | +/- 5% über 80 cm bei 30 cm Abstand |
Features & Benefits
Divergent Beam
From the plasma discharge, ions accelerate into a beam with a divergent ion current flux. The half maximum-half angle exceeds a 45º angle from the source axis. The divergent beam from an eH product covers a large area. The capability to uniformly cover a wide process zone facilitates high throughput operation, since a process run with a large load of parts or large substrate area becomes practical with an eH product.
Gridless
The eH product technology relies on a gridless construction. The ions accelerate directly from the plasma discharge to form the beam. The gridless eH technology complements our gridded ion source products, because it produces desirable beam properties not easily available with gridded sources. Other benefits of the eH gridless feature, include no need to maintain, align or replace grids. The eH products are rugged and simple to operate. And they typically cost less than their gridded counterparts.
High Density DC Discharge
The KDC products utilize a well-proven and efficient plasma generation process. In the discharge chamber, a cathode thermionically emits a reliable source of electrons. The electrons are attracted to a DC biased metal anode. The neutral gas species is efficiently ionized due to a confining magnetic field. This mechanism produces a high density plasma of many gases, including Ar, Xe, O2, N2 and other reactive gases.
Low Energy & High Current Output
The eH products output a high current and low energy beam. The high ion current meets critical arrival ratios for high process rates. Also, the high current enables productive processing on tough, hard materials. While the low energy ion bombardment eliminates damage to surfaces and interfaces. The capability to process at low energies has proven merit when working with delicate materials.
Non-immersed neutralizers
The standard KDC neutralizer configuration is an inexpensive refractory metal filament stretched across the ion beam. The filament is heated to thermionic emission temperature. The filament neutralizer may be replaced with an alternative non-immersed neutralizer. The non-immersed neutralizer sits to the side of the source and outside the ion beam. When the neutralizer is outside the beam, the time between maintenance is significantly longer for the non-immersed neutralizer versus the filament neutralizer. This non-immersed configuration is suited for low frequency maintenance installations and long operational runs when it is important to minimize the risk of process interruption.
Quick Change Anode Module
The eH Product incorporates our patented quick- change anode module assembly. The anode module can be quickly removed from the ion source for maintenance, while the source body remains in the chamber. The anode module is light weight and interchangeable. By simply exchanging the working anode module with a spare module, the eH product can be ready to run within minutes. The removed anode module can be easily maintained on a work bench while your vacuum chamber continues to be productive. The uptime benefits are significant.
Stable Neutralization
The product line provides a dedicated and regulated electron source neutralizer. With a reliable source of electrons, the products can process dielectric, electrically isolated, and electrostatic sensitive substrates. The amount of electrons is precisely controlled to match positive charges. The correct amount electrons are present in the ion beam and they arrive at the substrate surface to provide an electrically neutral process. The operation does not need to rely on an ambiguous source of electrons such as exposed and conductive chamber hardware. Coating build-up and stray electromagnetic fields, which may be present in the vacuum chamber, will not disturb the ion beam quality, stability or neutralization of the products. However, in the case, when the neutralization process is not so critical, the products do allow operation without the neutralizer.